
在因湃电池的工序中,智能监控能保证不良品零流出。
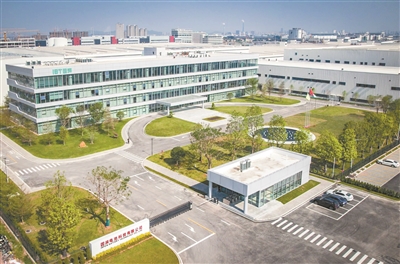
图为因湃电池工厂,位于广汽埃安智能生态第一工厂的南面。
跃上新高度
广州进行时②
2023年12月12日,在广汽埃安智能生态第一工厂南面,一座建筑外立面以白色为主色调的工厂建成投产,比最初规划提前四个月。
随后,这座工厂的第一批产品便经过小型物流车,运送到仅一墙之隔的广汽埃安智能生态第一工厂生产线,实现装车,进行大规模装车前的一系列测试。
该工厂名为“因湃”,投产之后,广州新能源汽车实现动力电池“自研自产”,产业链进一步可控,瞄准“万亿智车”之城,迈出一大步。
中国国际经济交流中心副理事长、商务部原副部长魏建国表示,目前广州新质生产力发展迅猛,齐头并进,整体优势凸显,有望涌现百亿级企业。因湃电池工厂满产之后,将实现200亿元产值。根据规划,第一工厂之后,因湃还将建设第二工厂。
近日,本报记者走进因湃电池工厂,进行实地参观和采访,了解广州汽车产业“电池+整车”联动生产的最新进展。
文/广州日报全媒体记者周伟力
图/广州日报全媒体记者吴子良
电芯车间要怎么打造
因湃电池打造电芯车间的“独门秘诀”,第一步是营造恒温、恒湿、防尘的生产环境,第二步则是减少无效空间、精简工作人员。“有人活动,就会产生尘土、带来静电;将无效空间最小化,在提升环境稳定性的同时,还能将维持环境稳定的能耗降至最低,进而降低生产成本。”因湃电池科技有限公司副总经理袁昊博告诉记者,在不影响生产和品质的前提下,因湃平均每生产1GWh的人员减少到99人,比行业平均的110人效率提升30%,能将对生产环境的干扰降到最低。
工厂空间要怎么利用
因湃电池工厂给人的第一感受是“满”。“尽可能在最小空间内,挤进更多机器”,实现效益最大化。
第二感受是“矮”,车间高度为4米,仅比工业机器人操作空间略高一点。现场作业,工程师是在机器丛林中定向“越野”,而非在平地里“路跑”。
第三感受是“准”,在狭小空间,机器手臂翻转腾挪,生产线分毫不差运转,其所带来的视觉感受相当新鲜。假如说整车制造是大开大合的“大写意”,电池生产则是精雕细琢的“工笔画”。
电池生产
解决卡点堵点 一直在抢时间
目前,因湃电池工厂调试和运行是电芯第一产线。与此同时,第二和第三条产线也提上日程。记者了解到,单线产能达到6GWh,比行业平均水平4GWh高出2GWh。这一成绩背后,是先进设备的启用、管理和人机协同,也得益于从源头就狠抓品质的精益生产模式。
“在采购时,我们和供应商一起,对设备不达标环节和参数进行改进。”因湃电池科技有限公司副总经理袁昊博表示,“目的是让生产以更高强度、更快节奏、更高效率进行”。
和整车制造不同,电池生产流程长,按“天”算。从最初粉末状原材料,到电芯,约需25天。“闲时很闲,忙时堵死”,这是电池生产一大痛点。“在电池生产企业中,因湃有整车制造经验,能让生产线运转更顺畅。”袁昊博表示。
电池核心部件是电芯。电芯“既怕冷又怕热,还怕潮和尘”。进入电芯车间,需要换装防尘服,并进行全身除尘。袁昊博介绍:“电芯车间环境堪比‘医院内科手术室’级别,PACK车间稍微低点,却也是‘医院外科手术室’级别。”
因湃电池工厂模组PACK工艺高级经理马朋超告诉记者,他现在和他的团队对模组PACK生产进行压力测试,“将所有卡点堵点解决掉,不能掉链子。”
投产不到一个月,因湃电池工厂已经收到来自广汽埃安的订单,为埃安和昊铂两个品牌旗下车型供应动力电池。在现场,记者留意到,因湃还着手准备生产体积稍小的动力单元,将用在广汽传祺插混车上。
新能源汽车市场瞬息万变。马朋超告诉记者,一直在抢时间。在设备导入阶段,他与团队一起,主动驻场,完成500多项检查,每天工作至次日凌晨,先后解决1600多项课题。“春节期间,调试会持续进行,工程师轮流休息。”
“智能化”是因湃工厂另一特点。因湃电池工厂工程师都是通过手持智能终端,即时了解、掌握生产线情况,结合设备屏幕,进行作业。与之相匹配的是源自广汽生产方式中的SSC理念(小型化,简单化,紧凑化),这种作业模式带来的好处显而易见,效率提升50%,设备投资下降超过30%。
在模组PACK车间,看不到现代工业大生产、悬挂在车间半空中的大屏幕,取而代之的是“数据共享”,人和人之间、人和设备之间、设备和设备之间、工厂和工厂之间,可以进行全天不间断的互联。
面向未来,因湃电池工厂将在2026年实现全新固态电池的量产。除固态电池,因湃电池工厂理论上还支持钠离子电池的生产。
成本优势
力跨三道难关 领先行业10%
市场瞬息万变,为进一步控制成本,广汽埃安选择走上电池自研自产之路。控制电池成本,要经历三关。
首先是工艺关,记者了解到,因湃经过技术攻关,解决行业4.5μm超薄铜箔涂布易断带、0.3mm铝壳焊接变形等一系列行业难题,顺利实现12μm超薄铝箔高压实投产。
第二道关是产品良率。电芯生产和堆叠速度快。“0.16秒就完成一次堆叠,靠人眼,已经看不过来,只能让设备来操作”。
“设备带有深度学习能力,不仅能做到监测,还能自主决策,并解决问题。”袁昊博介绍,单一产线建立1.5万+的数据采集和管控点,是同行的1.5倍以上,可实现的智能化应用场景增加35%。
因湃电池极片失效率降低至PPb级的行业标杆水平。“经过一系列测试和调校,年内产品一次性合格率有望达到95%,比过去行业最高水平还高出1个百分点。”袁昊博表示。
第三关是联动关。因湃电池工厂可以实现“研发—生产—装车”深度融合。袁昊博表示,“当一款电池研发出来之后,就可以模拟生产流程,并可以看见装车之后的性能表现,进而提升车载运营情况”“售后反馈和改良效率提升30%”。
那么,因湃电池工厂生产的电池到底能降低多少成本?袁昊博表示,因湃对成本的控制,将领先行业10%左右。
第一条生产线从来都是最难的,也将是2024年主要工作任务。电池生产,行业产能爬坡时间通常约需8个月,因湃电池工厂则压缩在4—6个月内完成。袁昊博表示,到今年中,第一生产线将满产;今年内,将有三条生产线投产。今年内,“将大批量供货,装车,数量是‘万辆’级”。